Main Targets
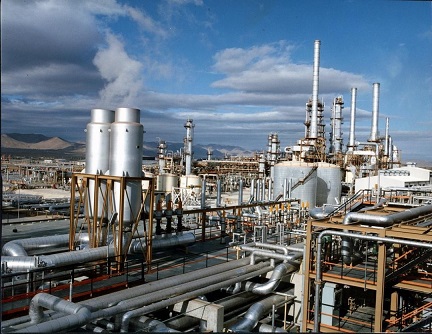
Urea & Ammonia Plants:
Urea is made from ammonia and carbon dioxide. The ammonia and carbon dioxide are fed
into the reactor at high pressure and temperature, and the urea is formed in a two-step reaction. The urea contains unreacted NH3
and CO2 and ammonium carbamate. As the pressure is reduced and heat applied the NH2COONH4 decomposes to NH3 and CO2. The ammonia
and carbon dioxide are recycled. The urea solution is then concentrated to give 99.6% w/w molten urea, and granulated for use as
fertilizer and chemical feedstock.
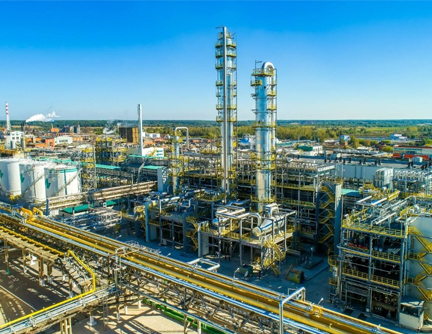
Methanol Plants:
Methanol is the simplest alcohol, consisting of a methyl group linked to a hydroxyl group.
It is a light, volatile, colorless, flammable liquid with a distinctive odor similar to that of ethanol. Methanol production with
methanotrophic strains is generally conducted in mineral media prepared in phosphate buffer with MDH inhibitors by adding electron donors.
Stable and low-cost chemicals, such as NaCl, may be more feasible for large-scale methanol production.
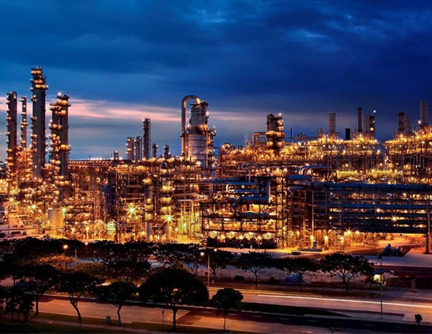
ETHANE CRACKER Plant & UTILITY Plant:
Ethylene is produced commercially by the steam cracking of a wide range of
hydrocarbon feedstocks. In Europe and Asia, ethylene is obtained mainly from cracking naphtha, gasoil and condensates with the coproduction
of propylene, C4 olefins and aromatics (pyrolysis gasoline). The cracking of ethane and propane, primarily carried out in the US, Canada and
the Middle East, has the advantage that it only produces ethylene and propylene, making the plants cheaper to construct and less complicated to operate.
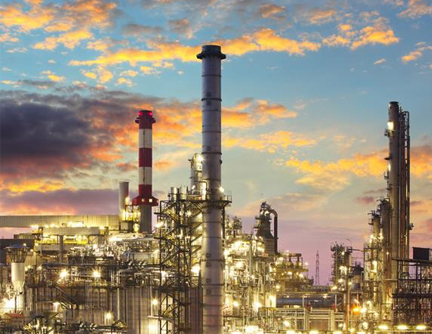
Polypropylene Plants:
Polypropylene belongs to the group of polyolefin and is partially crystalline and non-polar. Its properties
are similar to polyethylene, but it is slightly harder and more heat resistant. It is a white, mechanically rugged material and has a high chemical
resistance. The industrial production processes can be grouped into gas phase polymerization, bulk polymerization and slurry polymerization. All
state-of-the-art processes use either gas-phase or bulk reactor systems.
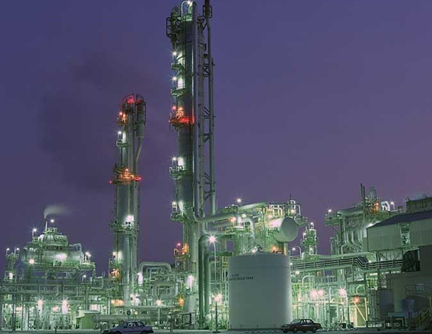
Linear Low-Density Polyethylene (LLDPE) Plants:
LLDPE is produced by polymerization of ethylene (or ethane monomer) with
1-butene and smaller amounts of 1-hexene and 1-octene, using Ziegler-Natta or metallocene catalysts. It is structurally similar to LDPE. The structure of LLDPE has a linear
backbone with short, uniform branches (unlike longer branches of LDPE). These short branches are able slide against each other upon elongation without becoming entangled
like LPDE. In the present day scenario, linear low density polyethylene (LLDPE) has been quite successful in replacing Low Density Polyethylene.
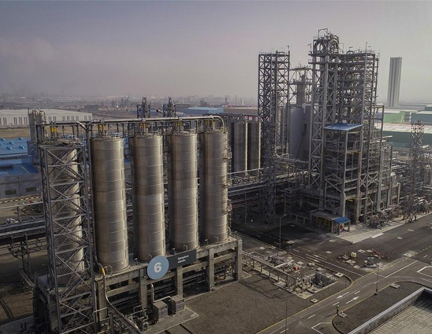
High-Density Polyethylene (HDPE) Plants:
High density polyethylene (HDPE) is a long-chain polymer or plastic. Polyethylene is
the most common form of plastic in the world and can be processed in a number of ways to make it thin, flexible, fluffy or strong and hard such as
with HDPE. HDPE is primarily used for wood-plastic composites such as plastic lumber. It is also blow molded to make plastic bottles, such as soda bottles.